Shop Talk: Load Cell Maintenance
Wednesday, June 10, 2020
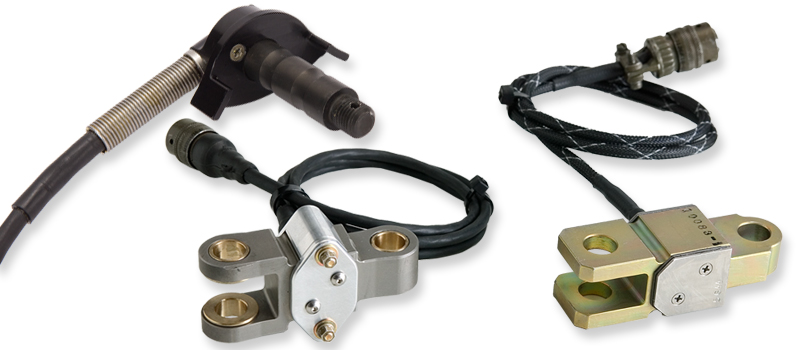
Onboard Weighing Systems provide operators with vital information about the weight they are carrying. Proper maintenance, including regular inspection and calibraton, is critical to ensure ongoing accuracy. All load cells have a specific schedule for factory service, which is documented in your user manual. As a general rule, you can anticipate the same factory inspection and service schedule for your Onboard Systems cargo hook and its associated load cell.
It is important to note that load cells are not field serviceable and must be returned to the factory for recalibration. Because the load cell gauges are delicate and can be easily damaged during disassembly, and because the calibration and zero balance procedures require specialized skills to perform with precision, there are no authorized service centers. Our standard load cell factory inspection service includes all recommended procedures listed in the owner's manual, including:
- Disassembly, inspection, cleaning, lubrication, and reassembly
- Replacement of all threaded fasteners, bearings, and bushings, as well as worn or corroded parts
- Inspection, repair, or replacement of the wire harness
- Performing any outstanding Service Bulletin compliance actions
- Resealing of the encapsulated electronics and recalibration
- Acceptance Test Procedures (ATP)
Discounted Load Cell Upgrades
As with all of our products, we are continuously improving our load cell assembly designs to take advantage of new technologies and safety enhancements. Some of the most recent load cell enhancements include:
- Stainless steel bodies for improved corrosion resistance in a wide variety of working environments.
- Improved sealant offers better protection for sensitive electrical gauges.
- Removable, easy-to-replace bushings have been incorporated into both attach points of the load link to extend the usable life of the system.
- Improved electrical harness has been upgraded to the more rugged M27500 series wire. We’ve also redesigned the strain reliefs for increased life of the cable.
When it’s time to send your older-style load cell in for overhaul, ask about our Load Cell Upgrade Program so you can take advantage of these improvements at a discounted price.
Load Cell Troubleshooting Guide
Finally, if you are experiencing problems with your Onboard Weighing System, we have an Electronic Load Weigh System Troubleshooting Guide available for download. This guide outlines field troubleshooting procedures for experienced aircraft mechanics using standard shop practices and basic troubleshooting skills. Initial troubleshooting is best done with the load weigh system installed in the helicopter. Standard shop tools and a quality volt-ohm meter are required.
As a general rule, difficulties with new system installations are usually associated with incorrectly setting up the cockpit indicator. Difficulties with the installation of new components (i.e. replacement load cell or cockpit indicator) are also due to cockpit indicator setup issues. Difficulties with existing installations are usually associated with cables that have been stretched, pinched, or cut and connectors that are damaged or corroded.
Tags
shop talkvol17-iss2load cellsMore Articles

Coatings & Finishes
You can extend the life of your Onboard Systems equipment with proper touch-ups for coatings and finishes that are damaged during use in the field.

Change in Hydraulic Fluid
Onboard has switched to MIL-PRF-87257 hydraulic fluid.

Load Cell & Indicator Troubleshooting Tips
How to determine if the problem in the load cell or the indicator?

Mechanical Release Cables
Get the 411 on mechanical release cable maintenance.

Storage and Inactivity
Got storage questions? Here are a few guidelines to assist you with preparing your cargo hook for storage or reinstallation.